Back in the 1970s, before the internet, I built a guitar in the workshops at school.
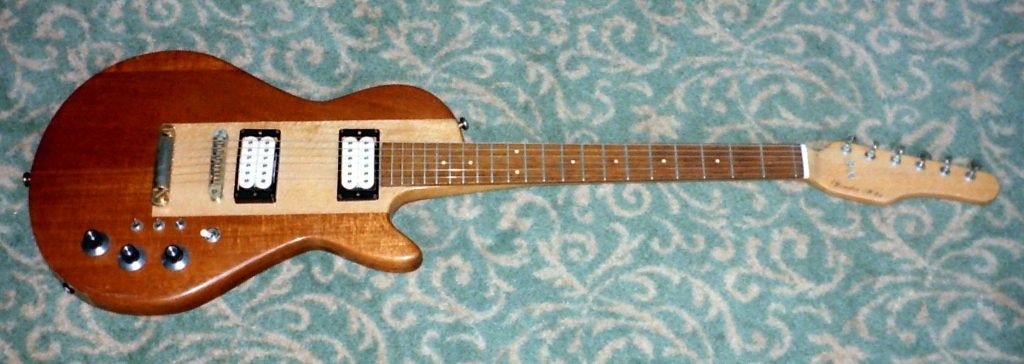
This is the result
The Guitar was hand made at the end of the 1970’s by myself from the bare wood, without recourse to prefabricated necks and bodies. It features a through neck, Schaller tuners and Di-Marzio dual sound pickups.
These days I would class it as a good piece of woodwork, but a fairly average guitar. Back in those pre-internet days it was impossible for a 16 year old school boy to glean the necessary knowledge. An article in a woodworking magazine, a stack of guitar brochures and hours spent examining the real thing in Liverpool music shops was all I had to go on. That and the advice and guidance of my excellent woodwork teacher, John Pie.
It is now pretty much retired, due to me acquiring much better factory built guitars. I do however hope to one day pass it down the family and hope that it turns up on antiques road show in 2106.
As a schoolboy I had an keen interest in music and had started to learn to play guitar, but it was hard going with my brothers cheap acoustic guitar. I had tried a friends electric guitar, and found it much easier to play. My family couldn’t afford one, so I dreamed on and persevered with the acoustic. Then my headmaster (principal) stepped in. He decided that the students in the sixth form would not spend the next two years with their heads in books. He resolved to make us do something practical and marched us over to the workshops. Here the woodwork and metalwork teachers were tasked with getting each of us to do a practical project. We all started something, but within a month everybody except me had dropped out. My project carried on for two years in parallel with my A level studies. The result is the guitar you see here, an A, two B’s and a D.
Scale | 24 3/4 inch (Gibson) |
Frets | 21 |
Pick ups | Di-Marzio Dual sound |
Length | 42 inches |
Width | 13 1/2 inches |
My main reference material was an article in a woodworking magazine for a simple “flying V” type guitar with a plywood body and a bolt on neck. Not very good really. The only thing I used from this was the overall neck dimensions and fret positions. This was 20 years ago, before the advent of the WWW, so I had little other information. I studied as many guitars as I could and perused catalogues in detail.
I based the body shape loosely on the Gibson Les Paul. The headstock owes more than a nod to the Fender Telecaster. I wanted a through-neck rather than a bolt-on, both for aesthetic and sustain reasons. The all over natural wood look is to my eyes very smart, so I avoided having a scratch plate. I did not particularly want a tremolo arm. I thought this would add unnecessary complication, so I went with a Gibson style “tune-o-matic” bridge and tailpiece.
Work started with the neck. This was shaped from a single piece of beech, kindly donated by a friend’s father. This was the key component in the guitar. The overall shape was marked out in pencil, based on the dimensions from the woodwork magazine article. Rough cutting out was done on the school bench saw. The next stage involved hours of laborious manual work with a spoke shave, rasp and sandpaper to get the neck profile right.
The fret board was a piece of rosewood from school stock glued to the neck and planed flat. Curvature was then introduced using sandpaper wrapped around a block. Fret positions were carefully marked, then cut with a fine razor saw.
Before the frets were fitted the position markers were added. These are lengths of plastic, cut from a large knitting needle and glued into holes drilled in the neck. When planed flat their origin is concealed.
Frets are made from commercially available fret wire, cut to just over length then forced into the appropriate saw cut in the fret board with a light hammer and a block of wood. When in place the frets must be correctly dressed.
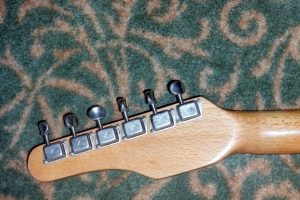
The machine heads and nut were fitted next. I used good quality Schaller machine heads. The nut is held in place by string tension. Two additional string trees were added to hold the thinner strings close to the head-stock and ensure sufficient break angle. With the addition of the bridge and tailpiece I could actually string the guitar.
At this point I had a playable guitar, even though it had no body and wasn’t very loud! The final job on the neck was to mark out and cut out the holes for two hum-bucker pick ups. The cavities were created using a bench drill and hand chisels. I didn’t have access to a router, this being a very exotic tool in the seventies.
The body is seeing it’s second lease of life as a musical instrument, being made from a school piano. I must emphasise that the piano had long since been decommissioned and stripped for useful material by the woodwork teacher. I didn’t leave Les Paul shaped holes in the side of the upright in the main assembly hall.,
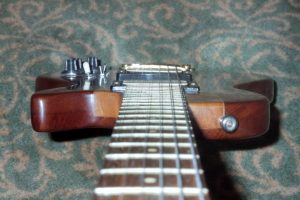
The body is a laminate of two pieces of mahogany to give the necessary thickness. The two were cut out at the same time on a band saw. The “top” piece then had the rectangular recess for the neck cut out carefully. The neck is actually thicker than half of the body, so the “bottom” piece was recessed to take the rest of the neck. This was done by careful work with a hammer and chisel, checking the fit regularly.
The “bottom” piece had an oval hole cut into it, which would form the recess for the electrics. This only gave a cavity half the depth of the body. I needed to achieve a wood thickness of only about 1/8 inch where the controls poked through the body. This was achieved by drilling small pilot holes from the front of the guitar where the controls (pots, switches) needed to be. I then turned the wood over and, using the pilot holes as a guide, drilled most of the way through the wood with a new sharp wide wood bit. This was done on a bench drill so that the depth of drill could be safely controlled using the drills adjustable stops.
The neck and both halves of the body were glued with Resin W and firmly clamped together over a weekend. Then followed another long session with the files, rasp and sand paper to shape the body so that it felt comfortable when held or worn. A key feature which took shape at this time was the smooth joint between the back of the neck and the body.
I now had a complete and working guitar, but it is in bare wood. Time to take it apart. Everything has to come off. All the fittings, pick ups, machine heads, knobs, etc.
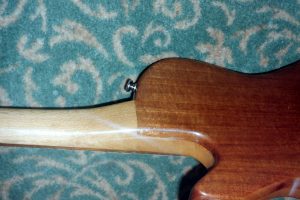
At first I tried a “Ronseal” type domestic varnish to protect the wood, but I found that such varnishes are not hard enough for this application. I discovered this the hard way and had to laboriously sand away all traces of the varnish.
The desired quality of finish was actually achieved by using “Rustins Plasticote” this is a two part finish. When the two are mixed a chemical reaction starts which culminates in a very hard surface, which can be polished to a mirror finish. Brian May used something similar on the “Red Special” I believe.
The key to obtaining a good finish is to apply multiple coats and sand down with wet & dry paper between each coat. There is no short cut.
Most guitars carry the makers name, mine is no exception. Lettraset was used to apply the legend “Yendor Mk I” on the head stock (read it backwards). This was done about half way through the finish coats, so that it benefited from the protection.
Final finishing is achieved by smoothing with a fine liquid abrasive, such as T-cut, then polishing with furniture polish.
Post Script
The finished guitar is pleasing on the eye, plays reasonably well, and has an acceptable tone. It is certainly much better than anything I could have affoded to buy at the time. However, with the benefit of hindsight, if I was doing it again I would pay attention to the following points.
- Woods
The body is good, being made of musical intrument grade mahogany. The neck however would have benefited from something like Maple. - Body thickness
The body is made of two layers. A third layer would have given it extra mass and probably improved the tone and feel. - Bridge position
I positioned the bridge too close to the fret board. At the time I did not appreciate the behaviour of stopped strings. Consequently there is insufficient backwards adjustment to be able to get the intonation quite right. - Truss rod
The neck does not incorporate a truss rod. Consequently I cannot adjust the action to be as low as I would have liked.